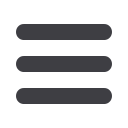
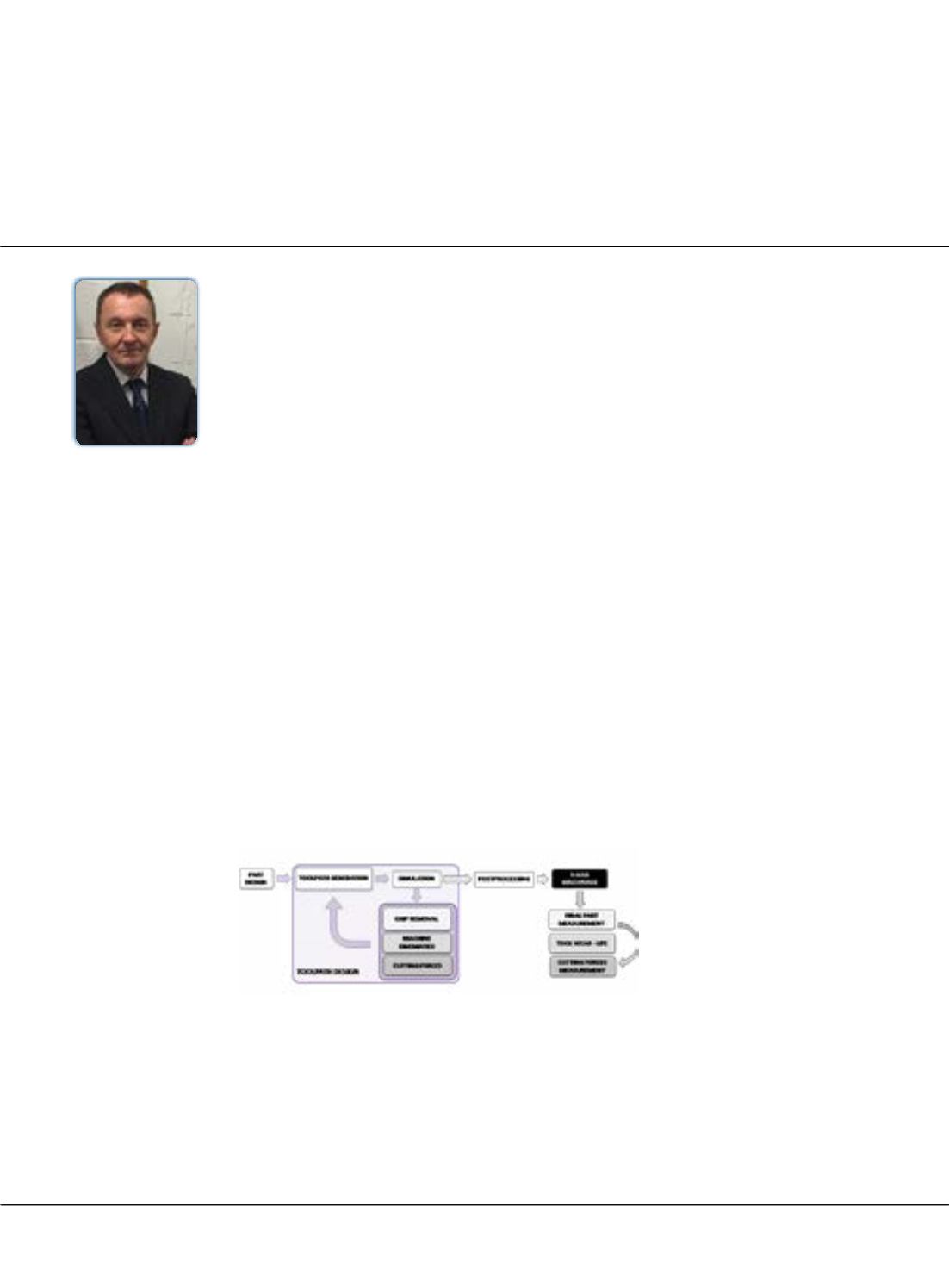
Volume 4
Nano Research & Applications
ISSN: 2471-9838
JOINT EVENT
October 04-05, 2018 Moscow, Russia
&
2
nd
Edition of International Conference on
26
th
International Conference on
Advanced Nanotechnology
Materials Technology and Manufacturing Innovations
Advanced Nanotechnology 2018
& Materials-Manufacturing 2018
October 04-05, 2018
Page 64
L N López de Lacalle
University of the Basque Country, Spain
L N López de Lacalle, Nano Res Appl 2018, Volume 4
DOI: 10.21767/2471-9838-C5-020
General methodology for manufacturing complex geometries in turbo-machinery components
A
eronautical industry is on the path to steady growth in the last decades. One of the major focuses for manufacturing
is turbo-machinery rotary components, such as impellers or bladed disks. The fabrication of these elements presents
many challenges to be faced from the designing conception to the arrival in the market. Among them, it is important
to point that they are made of difficult-to-cut super alloys and need to fulfill dimensional requirements. In Figure 1,
manufacturing process for complex geometries that require 5-axis simultaneously movements is shown. According to
the defined process for complex geometries, an IBR was selected as case of study for applying different steps with the
aim of establishing a full methodology to fabricate complex geometries. As workpiece material, Inconel 718 was selected,
common material in these applications. The proposed process was divided in the following stages: part design and
definition, according to industry requirements; tool definition and tool path generation. CAMsoftware is needed to define
5-axis simultaneous movements. A Calleja, et al. developed a model for tool path programming of these components.
Digital twin: Simulation of the full machining processes considering every machine component involved in the process.
A digital twin of machining process is developed with the aim of predicting collisions or machine kinematics limitation;
post-processing and 5-axis machining. Final part measurements and result analysis Not with-standing, improvement
in this area of knowledge leads many research to analyze about alternatives to this traditional methodology with new
manufacturing technologies, as electrochemical machining, linear friction welding, laser cladding or a new trend known
as super abrasive machining and new ways of lubricooling technologies as CryoMQL.
Recent Publications
1. Artetxe E, GonzálezH, CallejaA, PolvorosaR, LamikizAandLópez de Lacalle LN(2016)Optimisedmethodology
for aircraft engine IBRs five-axis machining. Int. J. Mechatronics and Manufacturing Systems 9:4.
2. Calleja A, Alonso M.A, Fernández A, Tabernero I, Ayesta I, Lamikiz A and López de Lacalle L N (2014) Flank
milling model for tool path programming of turbine blisks and compressors. Int. J. of Production Research: 3354-
3369.
3. Klocke F, Schmitt R, Zeis M, Heidemanns L, Kerkhoff J, Heinen D and Klink A (2015) Technological and
economical assessment of alternative process chains for blisk manufacture. Procedia CIRP 35:67-72C.