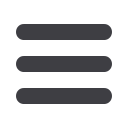
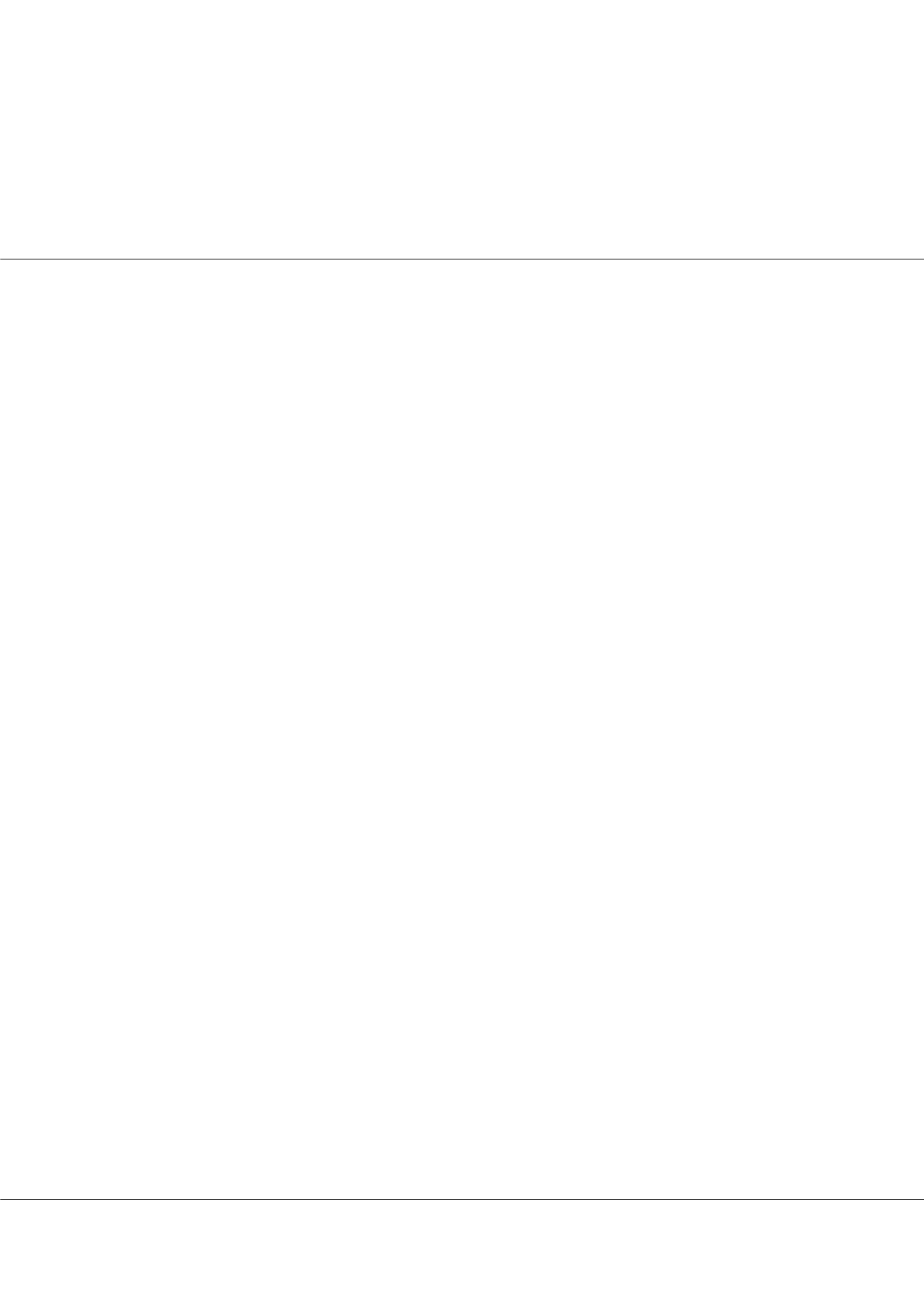
Volume 2
Journal of Environmental Research
Page 78
JOINT EVENT
July 26-27, 2018 Rome, Italy
&
6
th
Edition of International Conference on
Water Pollution & Sewage Management
4
th
International Conference on
Pollution Control & Sustainable Environment
Hydrothermal liquefaction of waste activated sludge to bio-oil using a continuous flow reactor
Chunbao Charles Xu, Laleh Nazari, Zhongshun Yuan
and
Madhumita B Ray
University of Western Ontario, Canada
T
his work presents experimental and Aspen simulation results on hydrothermal liquefaction (HTL) of waste activated
sludge (WAS) and co-feed of WAS and a woody biomass (rubber wood sawdust) in water-ethanol solvent (containing up
to 30 wt% ethanol) in a continuous flow reactor. The continuous flow process with the (0.15:1, w/w) wood and sludge mixture
at 310, 10 min hydraulic retention time and 12 wt% substrate concentration, produced a yield of 32 wt% bio-oil (dry ash-free
basis). Comparison of the oil yields in the continuous flow reactor with those from a batch reactor showed a slight decrease in
the yields. The HTL in water-ethanol mixed solvent led to a higher yield of bio-oil with a lower molecular weight, compared
to the oil produced in water alone. HTL bio-oil from WAS had high percentages of alcohols, amine and esters. The oil from
(WAS + wood) were found to be rich in phenols, attributed to the degraded lignin in the woody biomass. Thermal gravimetric
analysis of bio-oils showed higher volatile matters (VM) content (approx. 90 wt%) from WAS than that from the co-feed of
(WAS + wood) (VM content of approx. 78 wt%). Energy and mass balance calculations for the HTL process were performed
using Aspen Plus software and the experimental results. Based on the simulation results, the energy requirements of the HTL
process using co-feed of sludge and wood is slightly lower than that of the HTL of WAS alone. The energy demand of an HTL
process could be partly compensated by utilizing the HTL by-products (e.g., char or solid residue).
cxu6@uwo.caJ Environ Res 2018, Volume: 2