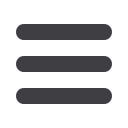
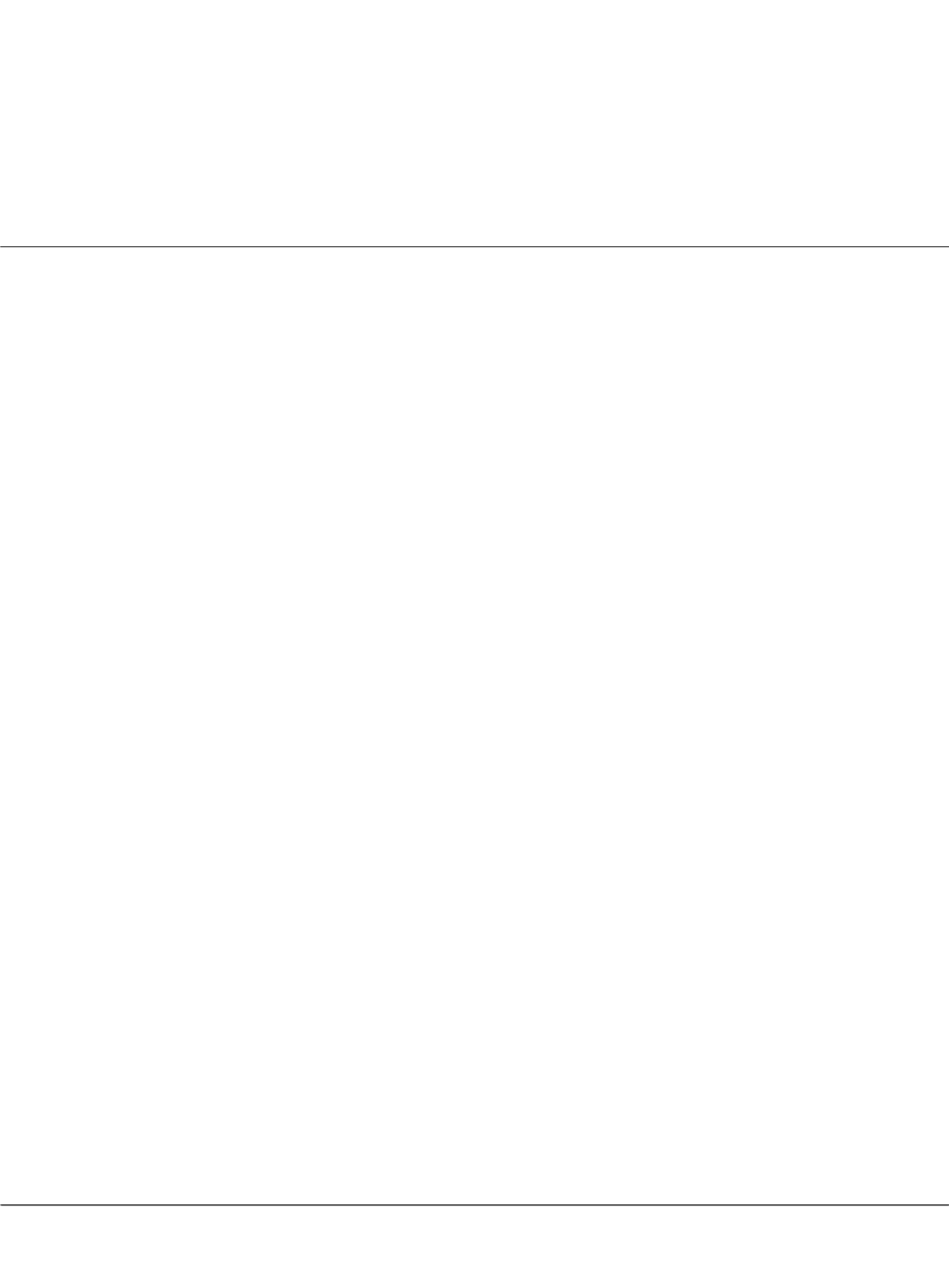
Volume 4
Nano Research & Applications
ISSN: 2471-9838
Page 90
&
JOINT EVENT
October 04-05, 2018 Moscow, Russia
2
nd
Edition of International Conference on
26
th
International Conference on
Advanced Nanotechnology
Materials Technology and Manufacturing Innovations
Advanced Nanotechnology 2018
& Materials-Manufacturing 2018
October 04-05, 2018
Development of mineral-filled polymeric membranes obtained by extrusion to implement in
separation by MEAUS procedure
Kian Habibi
Polytechnic University of Catalonia, Spain
M
icroporous membranes are commonly used in separation processes such as battery separators and medical
applications to control the permeation rate of chemical components. Due to the wide range of chemical structures,
optimum physical properties, and low cost of polymers and polymer blends, these materials are known as the best
candidates for the fabrication of microporous membranes. The two main techniques to develop polymeric membranes
are: solution casting and extrusion followed by stretching. High cost and solvent contamination are the main drawbacks
of the solution technique. Techniques to make porous membranes from polymers without using any solvent were
developed in the seventies of the last century for some applications, but most of the information on these processes
remains proprietary to the companies’ and are not available to the scientific community. One of the techniques is MEAUS
(melt extrusion annealing uniaxial strain). It is based on the stretching of a polymer film containing a row-nucleated
lamellar structure. Then, three consecutive stages are carried out to obtain porous membranes: creating a precursor film
having a row-nucleated lamellar structure by mechanisms of shear and elongation-induced crystallization; annealing the
precursor film at temperatures near the melting point of the resin to remove imperfections in the crystalline phase and
to increase lamellae thickness, and; stretching at low and high temperatures to create and enlarge pores, respectively. In
fact, in this process the material variables as well as the applied processing conditions are key parameters that control the
structure and the final properties of the fabricated microporous membranes. The material variables include molecular
weight, molecular weight distribution and chain structure of the polymer. These factors mainly influence the row-
nucleated structure in the precursor films at the first step of the formation of microporous membranes. Among a wide
range of resins, polypropylene (PP) is a well-known semi-crystalline polymer and, in comparison with polyethylene,
have higher melting point, lower density, higher chemical resistance, and better mechanical properties, which make it
useful for many industrial applications.
kianhabibi@yahoo.comNano Res Appl 2018, Volume 4
DOI: 10.21767/2471-9838-C5-021